Deep Dive into the Properties of Sewing Thread
"Tensile Strength", "Linear Density", & "Elongation at Break"
In our niche world of sewing, one of my favorite companies is the thread manufacturer Mettler, a company founded in Switzerland back in 1883. They are my go-to thread recommendation because they make high quality thread for a wide variety of applications at a fair price point. Recently, I was reading a Mettler product brochure and was intrigued by some terms they were using to describe their thread:
“Tensile Strength”
“Linear Density”
“Elongation at Break”
This edition of The Sewing Machine Newsletter will examine each of these terms in detail. These properties are crucial in determining how a thread will perform in different sewing applications, from durability to flexibility and suitability for various fabrics. By achieving a better understanding of these important thread characteristics, I believe that we can elucidate sewing thread in general— why certain thread is better for certain projects, why working with a specific fabric calls for a specific thread, how strong is a certain thread, how stretchy is a certain thread, etc.
I hope you find it helpful.
—Cale
Linear Density
Linear density refers to the mass per unit length of a fiber or thread. It is a critical measurement in the textile industry because it determines the thickness, strength, and performance of a thread. Different systems are used to express linear density, and Mettler provides values in Nm (Number Metric) and dtex (decitex).
Common Linear Density Units in Threads
Number Metric (Nm)
Definition: The number of 1,000-meter lengths of thread that weigh 1 kilogram.
Example: Nm 50 means that 50 kilometers of the thread weigh 1 kg.
Interpretation: A higher Nm number means a finer (thinner) thread, while a lower Nm number means a thicker thread.
Decitex (dtex)
Definition: The mass (in decigrams) of 10,000 meters of thread.
Example: dtex 150 means that 10,000 meters of the thread weigh 150 grams.
Interpretation: A higher dtex number means a thicker thread, while a lower dtex number means a finer thread.
Denier (den)
Definition: The mass (in grams) of 9,000 meters of thread.
Example: A 40 denier thread means 9,000 meters weigh 40 grams.
Interpretation: Like dtex, higher denier = thicker thread, lower denier = finer thread.
Tex
Definition: The mass (in grams) of 1,000 meters of thread.
Example: Tex 30 means 1,000 meters of thread weighs 30 grams.
Interpretation: A higher Tex number means a thicker thread.
Why Does Linear Density Matter in Sewing?
Thread Strength: Thicker threads (lower Nm, higher dtex) are generally stronger.
Sewability: Finer threads (higher Nm, lower dtex) work better for lightweight fabrics.
Appearance: The thickness of the thread affects stitch definition and seam bulk.
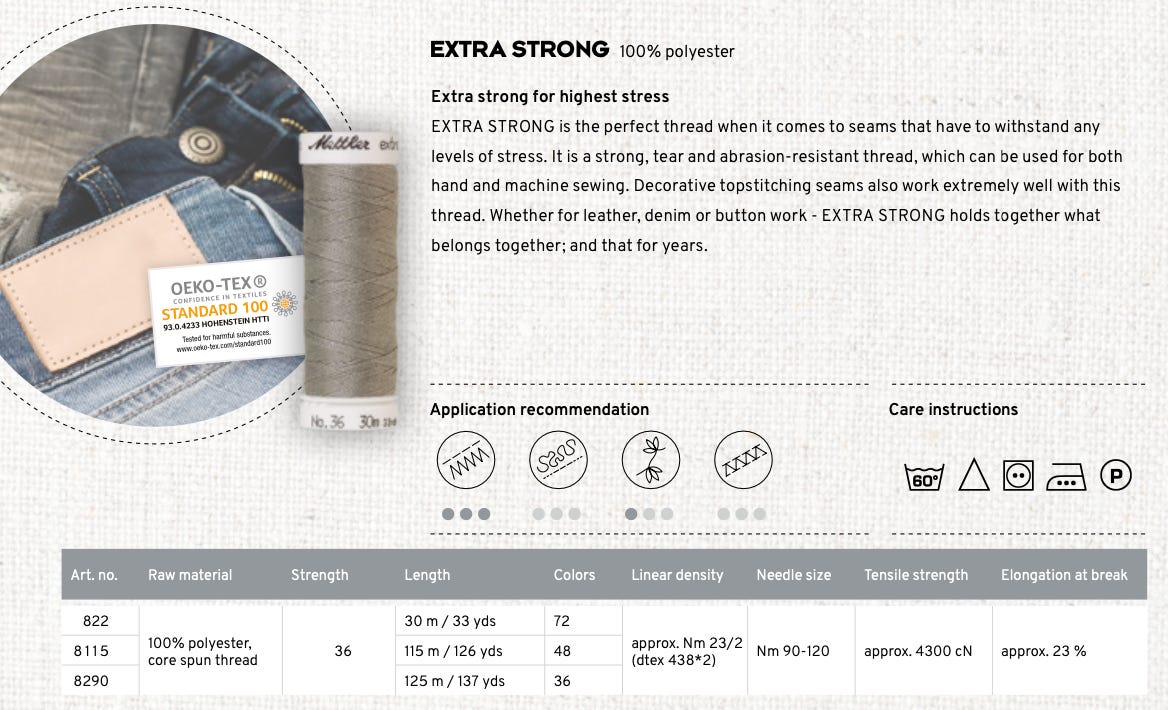
Tensile Strength
Tensile strength is the maximum force a thread can withstand before breaking when stretched. It is measured in centinewtons (cN), where 1 cN ≈ 1 gram-force.
For example: A thread with a tensile strength of 1,600 cN can withstand 1.6 kg (3.5 lbs) of force before breaking.
Why is Tensile Strength Important?
Durability & Load-Bearing Ability
Higher tensile strength threads can withstand more stress without breaking.
Threads with lower tensile strength may snap under tension.
Thread Selection for Different Applications
Heavy-duty sewing (jeans, leather, upholstery) → High tensile strength.
Lightweight fabrics (silk, chiffon, quilting cotton) → Lower tensile strength is acceptable.
Seam Strength & Longevity
A thread with high tensile strength ensures seams last longer.
Threads that break easily can cause premature seam failure.
How is Tensile Strength Measured?
Tensile Testing Machine
The thread is clamped at both ends and stretched until it snaps.
The force required to break it is recorded in centinewtons (cN).
Factors Affecting Tensile Strength
Material Type: Polyester is stronger than cotton.
Thread Thickness: Thicker threads generally have higher tensile strength.
Thread Construction:
Core-spun threads (e.g., polyester core with cotton wrap) are stronger than regular spun threads.
Filament threads (continuous fiber) are usually stronger than staple fiber threads (thread made from short, discrete fibers).
Comparing Mettler Threads by Tensile Strength
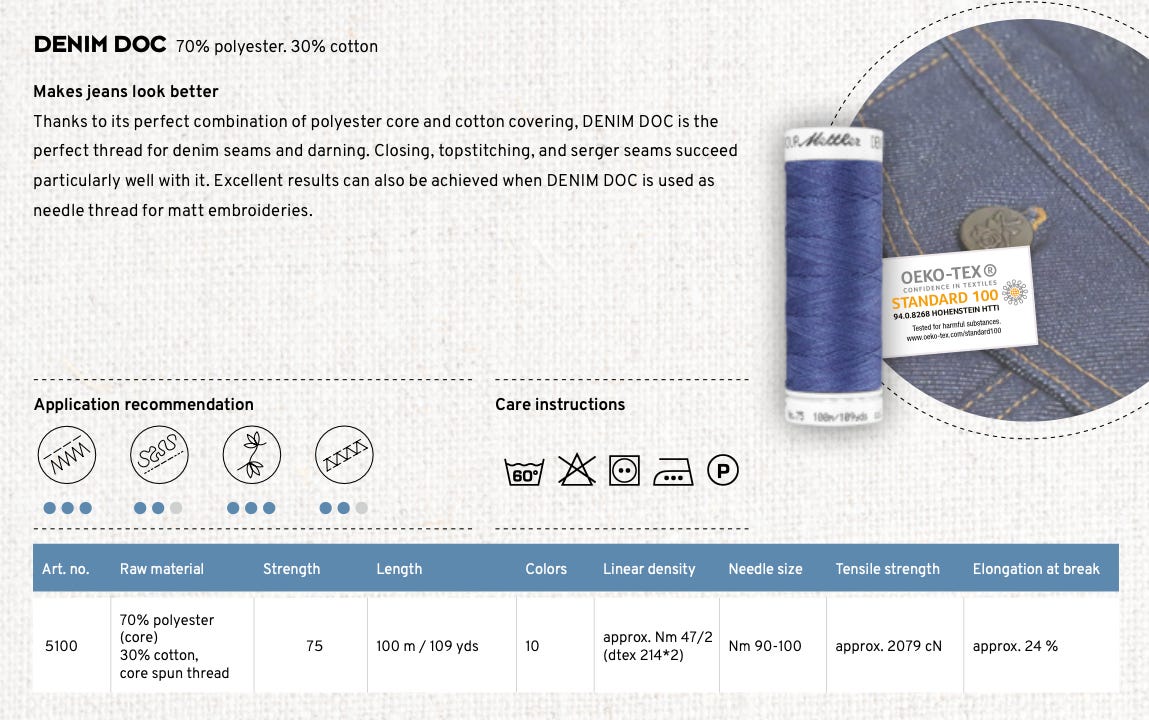
Choosing the Right Thread for Your Project
For Strong Seams (Jeans, Leather, Upholstery, Buttonholes) → High tensile strength (2,000-6,000 cN).
For General Sewing (Cotton, Polyester, Mixed Fabrics) → Medium tensile strength (1,000-2,000 cN).
For Decorative Sewing & Embroidery → Moderate tensile strength (~1,000 cN).
For Stretchy Fabrics & Activewear → Lower tensile strength (elastic thread) but high elongation.
Elongation at Break
Elongation at break is a measure of how much a thread can stretch before it breaks when subjected to tensile force. It is expressed as a percentage of the original length.
For example: If a thread is 100 mm long and stretches to 120 mm before breaking, its elongation at break is 20%.
Why is Elongation at Break Important?
Flexibility & Stretchiness
Threads with higher elongation are more flexible and stretchable.
Threads with lower elongation are more rigid and break more easily under tension.
Durability & Wear Resistance
Threads with moderate elongation can absorb stress and movement, making them ideal for garments and upholstery.
Threads with very low elongation are more brittle and may snap under tension.
Thread Performance in Sewing
If a thread stretches too much, it may cause seam puckering or loose stitches.
If a thread doesn’t stretch enough, it may break under high stress (e.g., in activewear or upholstery).
Typical Elongation at Break Values for Threads
How is Elongation at Break Measured?
Tensile Testing Machine
The thread is clamped at both ends and pulled until it breaks.
The machine records the change in length.
The result is expressed as a percentage of the original length.
Factors Affecting Elongation at Break
Material Type: Polyester and nylon have higher elongation than cotton.
Thread Construction:
Filament threads (continuous fibers) tend to stretch more.
Spun threads (shorter fibers twisted together) have lower elongation.
Thread Finish: Some coatings or treatments can alter elongation.
Choosing the Right Elongation for Your Sewing Project
For Strong Seams (Jeans, Leather, Heavy-Duty Sewing) → Lower elongation (less stretch, more stability).
For Stretchy Fabrics (Activewear, Knitwear, Lingerie) → Higher elongation (more flexibility).
For Embroidery & Quilting → Moderate elongation (prevents puckering but doesn’t stretch too much).
Article Summary
Tensile Strength – This refers to the maximum amount of tensile (pulling) force that a thread can withstand before breaking. It is typically measured in centinewtons (cN) and is an indicator of how strong the thread is.
Linear Density – This describes the thickness of the thread, usually expressed in tex, denier, or decitex (dtex). It indicates the mass of the thread per unit length, with higher numbers corresponding to thicker threads.
Elongation at Break – This refers to the percentage increase in length that a thread can undergo before it breaks under tension. A higher elongation percentage means the thread is more stretchable and resilient, which is particularly useful for flexible or stretchy fabrics.
These properties are crucial in determining how a thread will perform in different sewing applications, from durability to flexibility and suitability for various fabrics.
Thank you for reading!
I know this article was a bit dense, as an examination of these thread properties require that we dip our toe into the world of general material science and textile engineering. I hope you found it helpful.
If you want to take a look at the Mettler product brochure that inspired me to take a deeper look at thread properties, I will attach the PDF below.
—Cale
An interesting subject, and something I've been thinking about lately.
In college we learned that is was preferable to have thread slightly less strong than the fabric. If your jacket pocket gets caught on something you want the seam to rip, not the fabric. And during the time I worked as an alterations and mending tailor, the vast majority of mending was from fabric failure, not thread failure. It happened, particularly on stretch fabric, but mostly I dealt with patching and such.
I guess it probably depends on the sewn item. I have had thread wear away faster than the tough performance fabric on some bags. But on my cotton flannel robe the fabric was damaged years before the thread was.
I am surprised to learn that nylon has high elasticity. The 69 bonded nylon I use for leather feels completely unstretchable, unlike Mara 100 (for example)
Many of us have large stashes of threads as well as fabrics. The thread does not retain its strength forever though. I’ve tried stretching the some older threads a bit and it snapped immediately especially the cotton ones. Is there a shelf life for thread? What do you recommend for checking the thread’s condition? Thank you.