If you are getting skipped stitches all of a sudden and you don’t know why, the first thing you need to do is remove the needle that is currently in your machine and insert a new needle. It doesn’t matter if you changed your needle 5 minutes ago, 5 days ago, 5 months ago. A bent needle is the #1 cause for skipped stitches and there isn’t a close second. In this edition of The Sewing Machine Newsletter, I am going to delve into the details explain exactly why this is the case.
The function of a sewing machine is to stitch cloth together by tying a knot with two sources of thread (the upper thread spool and the bobbin thread). The successful formation of that knot is absolutely critical to the stitch-making process. Regardless of what machine you have, the knot is formed below the needle plate, when the needle goes down below the needle plate hole.
As you sew, the needle goes down and the needle goes up, over and over again. As the needle the goes down, the upper thread that you’ve threaded through the needle eye is taught. When the needle goes down below the needle plate and reaches its bottom-most position— what sewing machine technicians call bottom dead center— the thread is still taught. But, as the needle begins its path upwards, a loop is formed just above the eye of the needle.
In the video below, pretend my bottom hand is the eye of the needle and the belt is the thread. As the needle/hand travels downward, the thread/belt goes down with is. The needle reaches the bottom-most position, then begins to travel upward. As the needle begins its upward trajectory, the thread forms a loop.
As this loop is formed, the hook point of the sewing machine’s hook mechanism comes along and passes through thread loop. The hook point catches the needle thread and takes it along a 360 degree path around the bobbin case. While riding along this path, the upper thread forms a loose knot with the bobbin thread. Then, as the needle reaches its high point, the action of the take-up lever cinches the knot (formed below the needle plate) up into the fabric we are sewing. That, in short, is how a successful stitch is made.
As it pertains to this article, the critical point in the process explained above is when the needle passes through the thread loop formed at the eye of the needle. A sewing machine is engineered so that the hook point passes behind the needle just above the needle eye, right as the the needle has begun its upward trajectory, about 2-3 mm above bottom dead center. What happens if the hook-point doesn’t pass just above the eye of the needle right as the thread loop has been formed? The hook-point won’t catch the upper thread loop, won’t take the upper thread around the bobbin case, and the upper thread and bobbin thread won’t have a chance to form a knot. In other words, you get a skipped stitch.
Why wouldn’t the hook-point pass through the thread loop? It could be that the timing is off. If you’ve ever heard a technician say the machine’s timing is off, they most often mean the needle-hook timing is off. The timing could be advanced— meaning the hook-point behind the eye of the needle too early, before the thread loop has been formed. Or it could be that the timing is retarded— meaning the hook-point passes behind the eye of the needle too late, when the thread loop is out of reach.
However, more often than not, when a machine is skipping stitches, the needle-hook timing is perfectly fine and a bent needle is the culprit. Whether it’s bent to the left or bent to the right, a bent needle will mimic out of whack needle-hook timing.
Imagine you are facing your machine and the needle is bent slightly toward your right. With the needle bent to the right, the eye of the needle has been moved slightly toward the right. Therefore, the hook-point will arrive at the needle too early, before the thread loop has had a chance to form (mimic advanced timing). The result: skipped stitches. The same goes for a needle bent to the left. A needle bent to the left means the eye of the needle is moved to the left. In this case, the hook-point will arrive at the needle eye too late, when the thread loop is out of reach (mimic retarded timing). The result is the same: skipped stitches.

Okay, so maybe I am getting skipped stitches, so I take the needle out of my machine, lay it on a table and look at it carefully. As far as I can see, it’s not bent to the left and it’s not bent to the right. I emit a primal scream. Frustration arises in my soul! What the heck is going on?!?!
Then I remember: the needle could be bent to the front or back, which isn’t so easy to see, but is just as common. What happens if the needle has a slight bend to the front or back? Whereas a needle bent left/right mimics faulty needle-hook timing, a needle bent front/back mimics faulty needle-hook clearance.
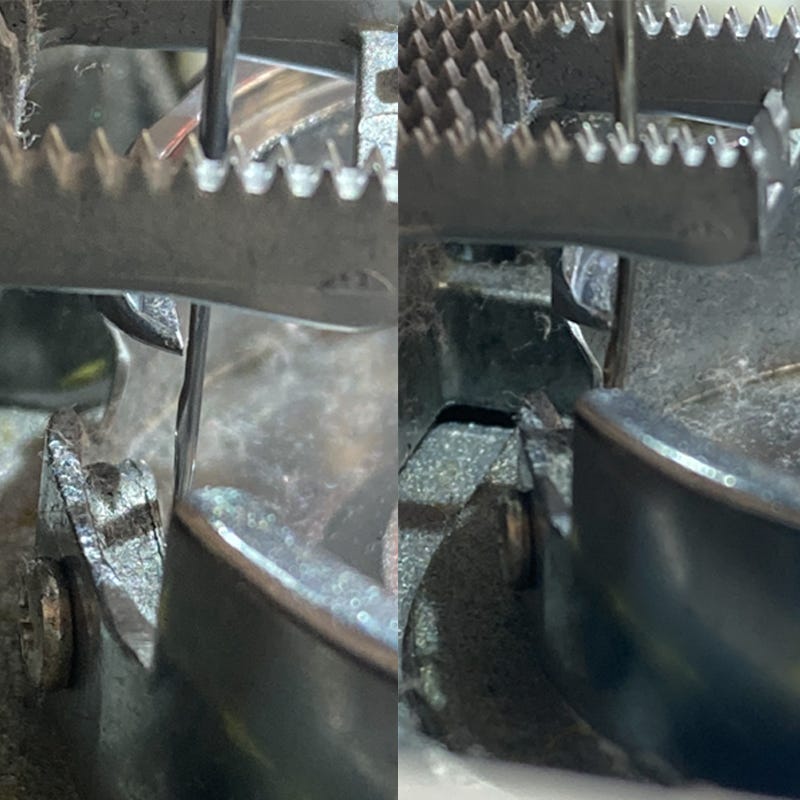
Remember the critical moment in the stitch-making process I stressed earlier: the hook-point passes right behind the needle and catches the upper thread loop, just as the needle is a couple millimeters above bottom dead center. Well, when the needle passes behind the needle, it must do so at a specific distance away from the needle.
Imagine you are facing your machine and the needle is bent slightly forward, towards you. As the hook-point passes behind the needle, it will pass too close to the needle— in fact, in some cases, the hook-point will actually make contact with the needle. This is not ideal. If your needle is bent in a manner that causes the hook-point to deflect off the needle, the machine’s ability to consistently make a stitch is compromised and occasional skipped stitches will likely occur. The opposite is also problematic. If you are facing your machine and the needle is bent slight backward (away from you), then the hook-point will pass too great distance away from the needle. The thread loop will be formed at the needle eye, but the hook-point will be too far a distance behind the needle to catch the loop consistently.
In Review:
If the hook-point fails to catch the thread loop, a skipped stitch will occur 100% of the time.
If you get a skipped stitch, remove the needle that is in your machine and insert a new needle. Most of the time this will solve your problem.
If skipped stitches still occur, the second thing to consider is if you are using the right needle type for the fabric you are sewing (e.g. stretch needle for stretchy fabric, a jeans needle for denim) (I will explain why this is crucial in a later article).
If your machine is still skipping after all that, call you preferred sewing machine dealership. A trained technician may have to open up your machine and adjust critical settings. There are other things that can cause a skipped stitch that I hope to cover in the future articles.
There is very little room for error when it comes to sewing machines. They are complex pieces of machinery, and you all deserve a pat on the back for being able to operate them mostly successfully and use them to be creative and express yourself. I hope you found this article useful and that you can use this knowledge to help you get over a skipped-stitch speed bump in the future.
Any feed back you have would be much appreciated! This article was experimental in the sense that I went into much more detail about a critical concept than I normally do in our store’s regular newsletter. Did you find this article useful? Do you feel like you learned something new? Did I bore you? Suggestions on subject matter to cover in the future? Your honest opinion will not offend me, I will use it to improve The Sewing Machine Newsletter in the future!
Great article and so useful.
Question, and please, I am trying not to offend: You used the word "taught," which implies teaching; did you mean "taut?" I looked up your usage because it looked off, but also found this.
Taut means tight rather than slack. It sounds like the word "taught" and means stretched tight, like a rope, muscles, or even nerves.
I bought a subscription and look forward to more articles!
Very informative, ty