Greetings everybody,
In this edition of The Sewing Machine Newsletter, I will talk about the various problems that can occur from sewing with poor-quality thread.
Before I start, I want to quickly note that I am coming at this from the perspective of somebody who sells and repairs sewing machines. I am not a quilter or crafter. I do not make my own clothes or sew as a hobby. My primary concern is stitch quality, since a big part of my job is to make sure that the sewing machine is performing to the best of its ability.
Loop Creation
When I think of the engineers who design sewing machines, I imagine a chief concern of theirs was “how do we get the machine to consistently create a thread loop?” Loop creation is a vital aspect of how a sewing machine makes a stitch. If the loop is not created properly, your machine will skip stitches.
Think of it like this:
The function of a sewing machine is to stitch cloth together by tying a knot with two sources of thread (the upper thread spool and the bobbin thread). Regardless of what machine you have, the knot is formed below the needle plate when the needle goes down below the needle plate hole, where the bobbin thread is laced through the upper thread loop.
As you sew, the needle goes down and the needle goes up, over and over again. As the needle the goes down, the upper thread that you’ve threaded through the needle eye is taut. When the needle goes down below the needle plate and reaches its bottom-most position— what sewing machine technicians call bottom dead center— the thread is still taught. But, as the needle begins its path upwards, a thread loop is formed just above the eye of the needle.
Just as this thread loop is formed, the hook point of the machine’s hook mechanism comes along and passes through thread loop. The hook point “catches” the thread loop and takes it along a 360 degree path around the bobbin case. While riding along this path, the upper thread forms a loose knot with the bobbin thread. Then, as the needle reaches its high point, the action of the take-up lever cinches the knot [formed below the needle plate] up into the fabric we are sewing. That, in short, is how a successful stitch is made.
In the video below, focus on the thread loop that forms above the needle eye, and how the hook point passes through the loop in order to make a stitch:
If you use good quality thread, that thread loop will form properly every time. It will form at the point that the engineers intended it to form, which is just above the eye of the needle when the needle has risen a couple millimeters above bottom dead center.
Poor quality thread can possess certain characteristics that potentially cause a distorted loop. Imagine that we are using thread that is especially stiff and it takes a longer time for the loop to form. When the hook point passes above the eye of the needle, that thread loop could be extremely narrow because the loop has yet to fully form— more like a slit than a loop. In this case, the chance that the hook will will successfully pass through the loop is low. Or, imagine that the thread is sticky or strange in some other type of way. Instead of forming a loop, it sticks to itself and twists into a figure-eight or some other weird shape. This is not conducive for success; it is conducive for skipped stitches.
ANALOGY:
The thread loop is like an open doorway, and the hook mechanism is a person looking to walk through that door. With quality thread, the doorway is where it should be and a person can walk through with no issues whatsoever. Poor quality thread causes the doorway to be 5 feet off the ground, or slanted at a 45-degree angle to the right, or distorted down to a minuscule passageway that is impossible to squeeze through.
Thread Shredding & Breaking
Another problem with poor quality is that it is more prone to shredding and breaking. There are a handful of reasons why this is the case, but most often it is either because the thread is brittle, or because it is getting snagged on places it shouldn’t due to it possessing those strange characteristics I mentioned in the previous section.
Take a look at your sewing machine and notice the path of your upper thread when you thread the machine. Not only is the thread constantly under tension sandwiched between the tension discs, it also makes contact with many different parts of the machine whose surface area is made of plastic or metal.
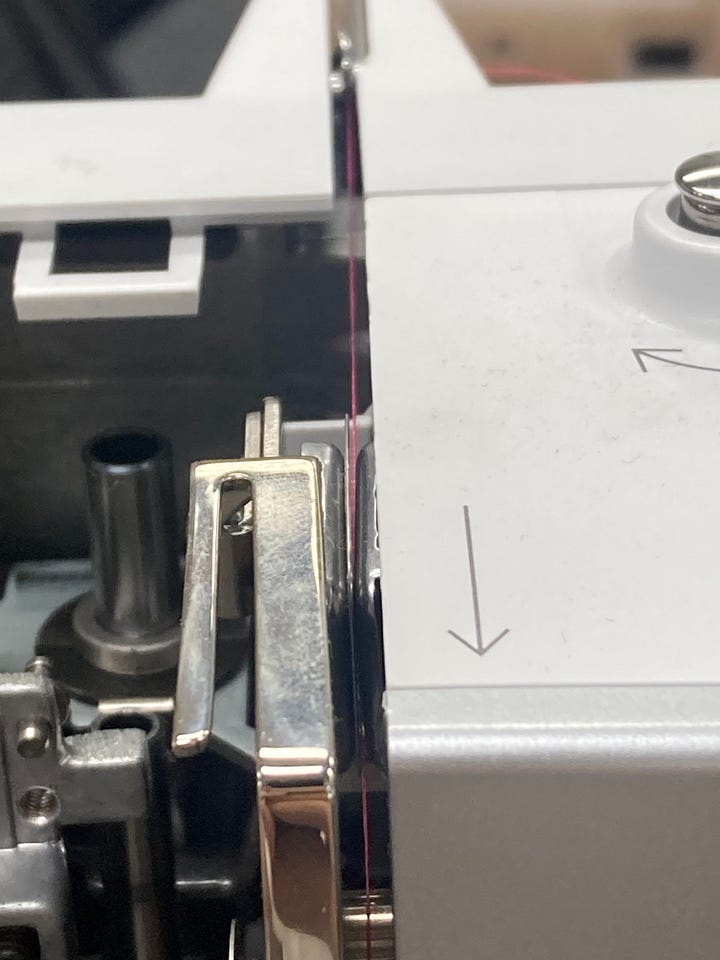
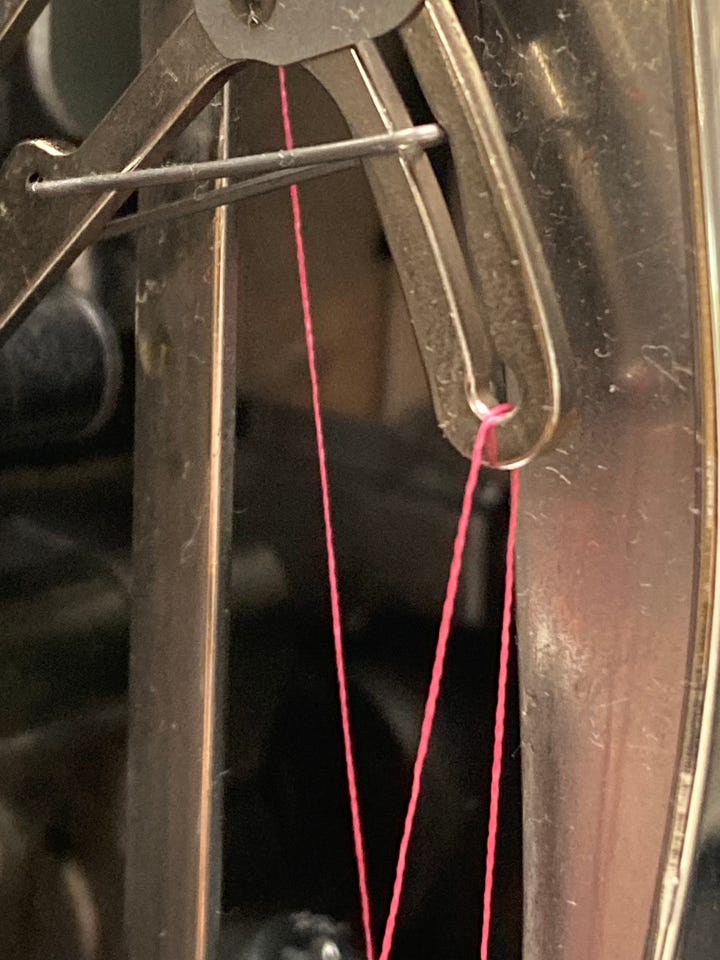
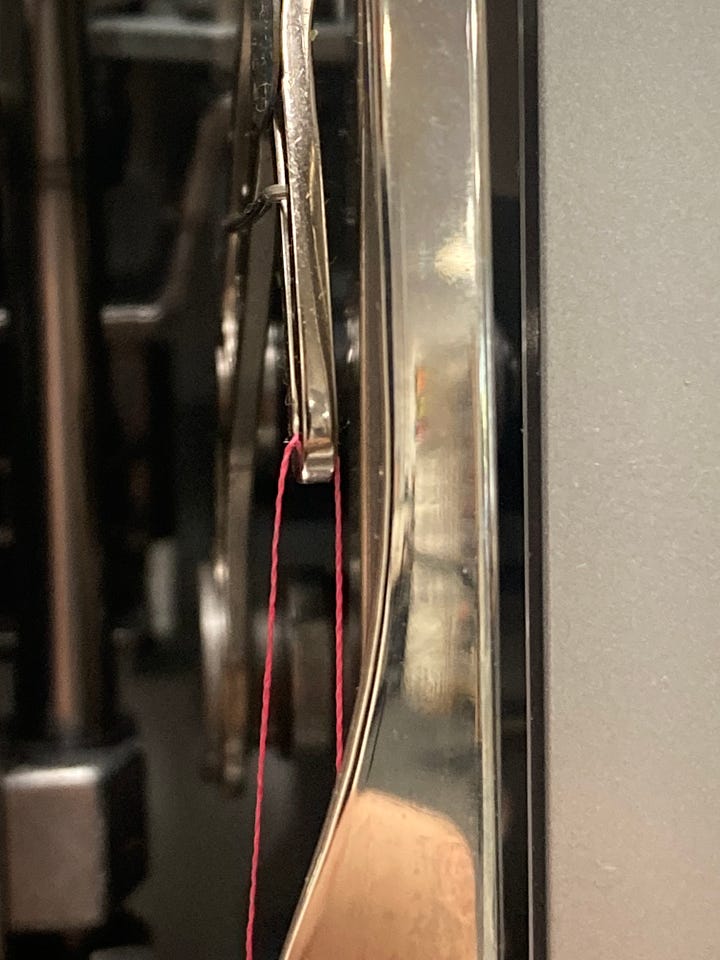
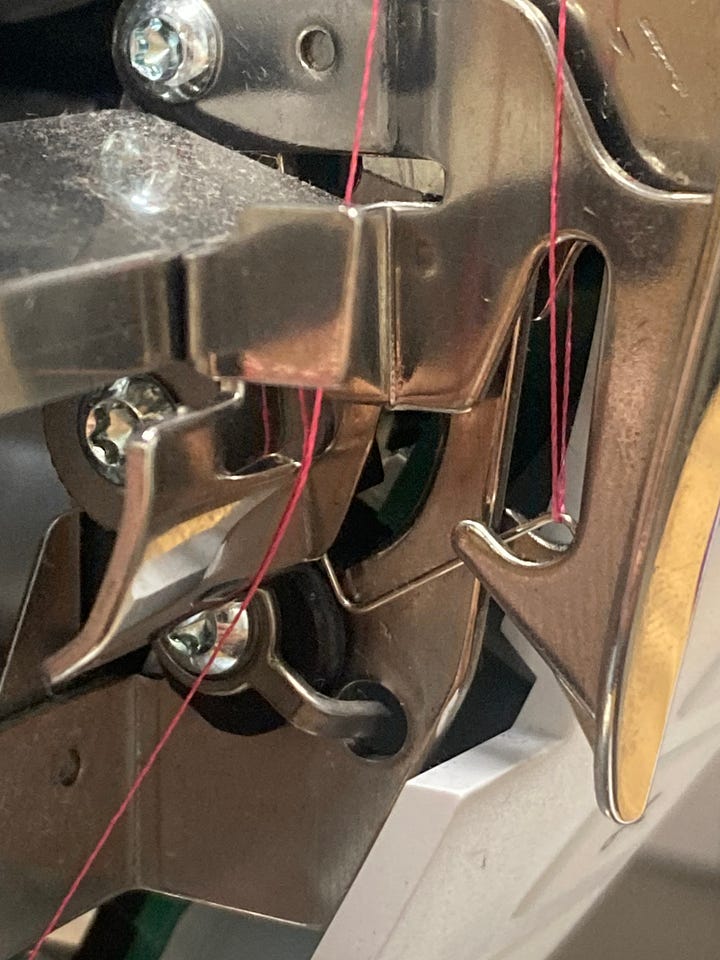
Meanwhile, underneath the needle plate, the thread passes over the bobbin case and hook mechanism during every stitch, which you can see in the video below:
In addition, the upper thread is constantly passing through the biblically tiny needle eye:
I bring all of this up to make a point. There are many points on the sewing machine where the thread makes contact with a hard plastic or metal surface. While all thread is relatively thin and prone to breaking or shredding, some thread is more prone than others. The engineers who design these machines take pains to make these contact points smooth and “thread-friendly”, but they cannot overcome old brittle thread, or strange thread that is overly stiff or sticky. I have had countless experiences where someone comes into the shop with the complaint that their thread is shredding or breaking, then I thread up the machine with good quality thread and the problems never repeat themselves.
Tension Issues
I have already described poor-quality thread as having certain characteristics that are generally undesirable— being unnecessarily stiff, sticking to itself, being uneven, possessing kinks, etc. A thread like this will have greater drag when passing between tension discs if compared side by side with good-quality thread. Increased drag will cause tension issues.
Remember, a sewing machine uses two sources of thread to make a stitch— the upper thread spool and the bobbin thread. Both of these thread sources constantly pass between enclosed metal discs as we sew, which puts the thread under tension. You can imagine, a thread that is particularly coarse or sticky or possesses random kinks and unevenness— all of these undesirable characteristics will affect the thread tension.
I have noticed that bobbin case tension is particularly affected by poor quality thread, which makes sense because the bobbin case tension discs are far more delicate and sensitive than the upper tension discs. Because of the greater drag on the bobbin case tension, the knot will often sit on the underside of the fabric. To combat such an ugly stitch, the sewist is forced to crank up the dial of their top-thread tension discs, even though that tension is already really tight due to increased drag of bad thread.
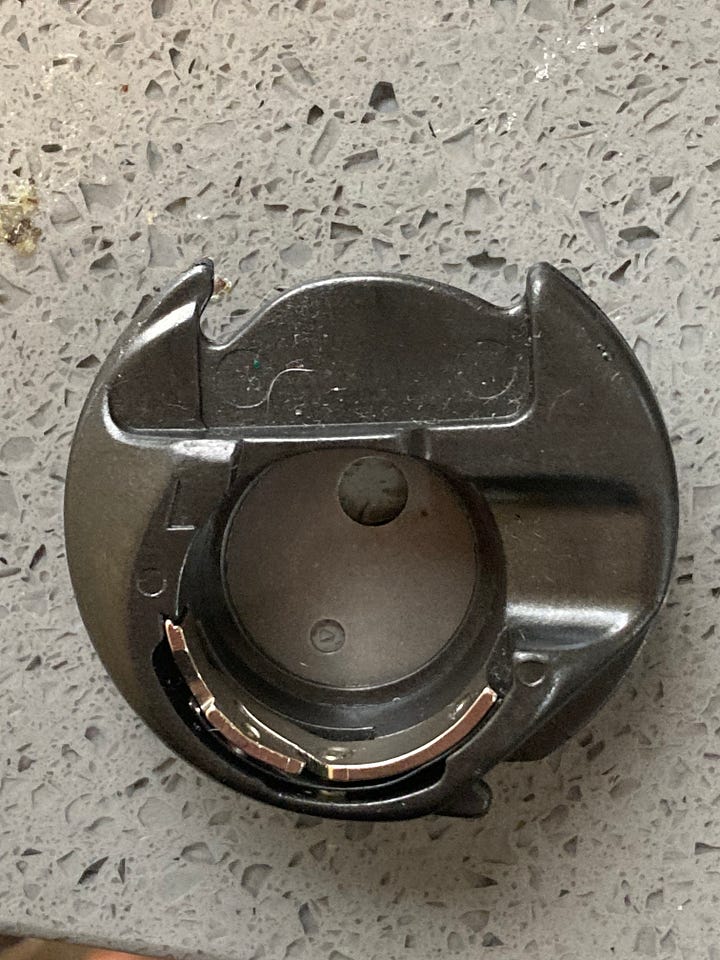
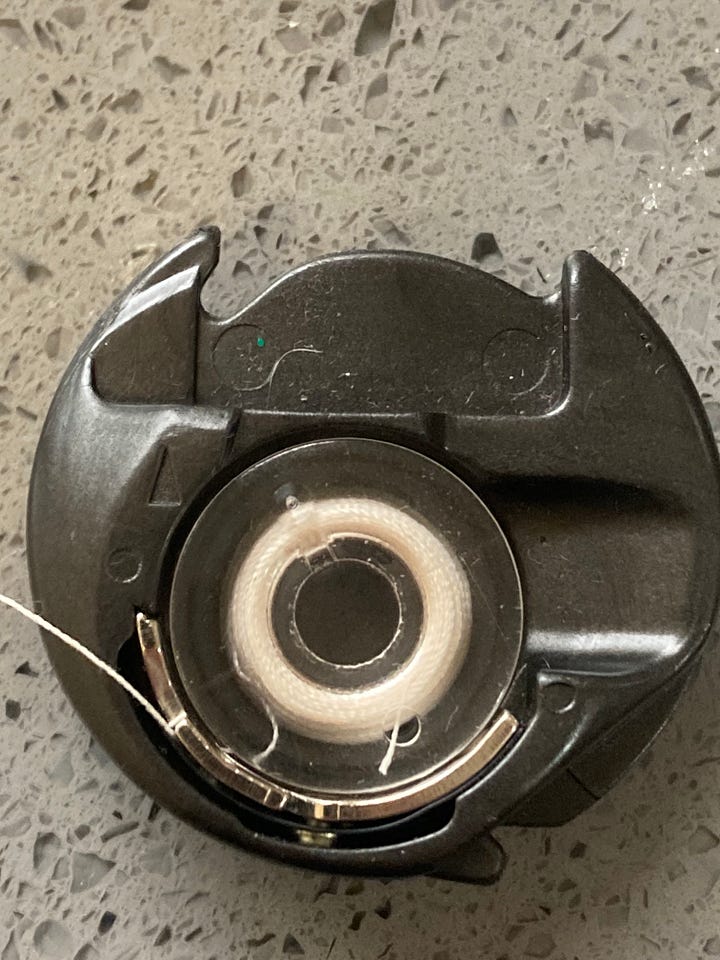
I may sound like a broken record, but I have seen this issue countless times where someone brings in their machine because it will only make a stitch with the upper tension dial cranked up to 8-9. When I rethread the machine with thread I know to be of good quality, the problem goes away.
Thread Brands I Know To Be Good
I don’t want to go talking bad about certain brands of thread, because I honestly don’t have a lot of experience with them. I’ll make a couple of generalizations— again, from my perspective as a technician, not a sewist:
The cheapest thread you can buy at a place like Joann’s is typically poor quality. As the saying goes, you get what you pay for.
Old thread, such as the kind you see on wooden spools, is especially susceptible to shredding and breaking. Thread does have a shelf life.
Here are the brands I know to be good:
Mettler - both their cotton and poly are good and relatively inexpensive
Aurifil - beautiful Italian cotton thread
Maxilock - particularly great for sergers
Isacord - particularly great for embroidery
Intressa - UV-rated thread, good for outdoor use
King Tutt - variegated thread, especially beloved by quilters
Thank you for reading
When it comes to thread breaking and shredding, skipped stitches or ugly stitch quality, I cannot understate the importance of using quality thread. Seriously, you could have a top-of-the-line machine with a fresh needle, sewing on an incredible swathe of fabric— none of that can overcome bad thread.
I troubleshoot sewing machines every day at work and often get accused of performing magic because I will sew on the customer’s machine and cannot repeat their stated problem. The truth is that there is no magic at play (most of the time). I simply insert a fresh needle and re-thread their machine with quality thread.
Thank you for reading,
-Cale
Thanks for another interesting issue. Could you add commentary on the proper way(s) to mount upper thread depending on whether the spool is cross-wound or not, and comment on how to minimize unneeded "twisting" tension in thread? (same general comment on the importance of bobbin thread directionality in the bobbin case). I've found these can make a big difference, and since I use alot of different vintage sewing machines (and modern), I need to keep careful watch of these issues.
No to be overdramatic, but you have just solved one of Life's Great Mysteries for me - how the heck does a sewing machine work? I know there are many other complexities, but the simple formation of a stitch under the needleplate has always been something my mind could not figure out. Thank you!