How to Properly Insert a Sewing Machine Needle
Improper needle insertion can cause all sorts of problems.
Previously, we have covered things like needle type and needle size. . . .
But today, I simply want to cover a few keys to proper needle insertion.
(1) Flat to the Back
If you look at the base-end of a home sewing machine needle, you’ll notice that one side is round and the other side is flat.
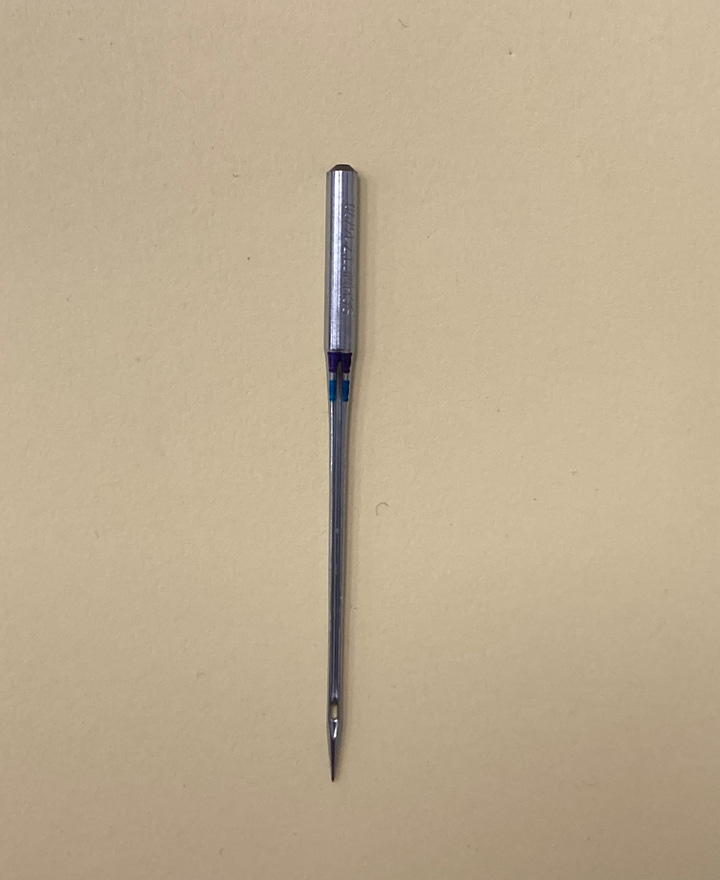
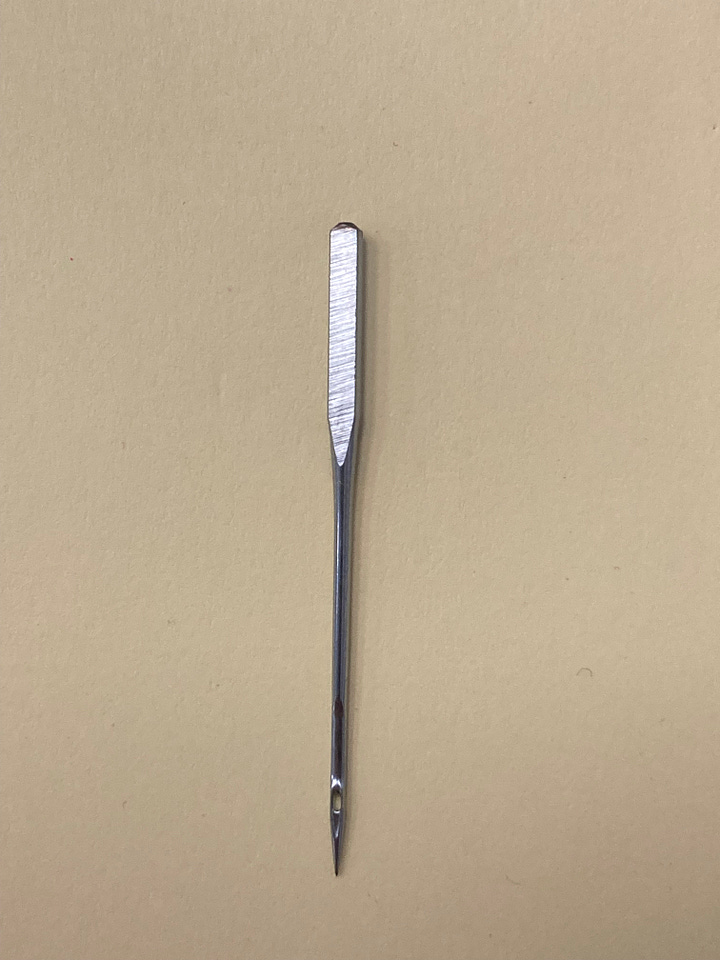
On the vast majority of home sewing machines, you must insert the needle with the flat side facing the back of the machine. Or, another way to think of it: the flat side faces away from you and the round side faces toward you. Either way, the flat is to the back.
A notable exception to this flat-to-the-back rule is the Singer Featherweight, in which the flat must face the left.
Other notable exceptions include all the portable semi-industrial straight-stitch machines, where the flat side of the needle faces the right: Juki TL-2010, Juki TL-18, Janome HD9, Janome 1600P, Bernette B08, Brother Nouvelle, Baby Lock Accomplish, Pfaff Grand Quilter, Viking MegaQuilter, etc…. because these machine designed with side-loading bobbins, the flat faced the right.
Why is it important that the flat side of the needle faces the correct direction?
When a sewing machine makes a stitch, a thread loop forms behind the eye of the needle as the needle begins to rise upward from its bottommost position. As that thread loop forms, the machine’s hook passes behind the needle, just above the eye, and catches the thread loop.
There is a cut-out, or a scarf, on the backside of the needle above the eye. When we insert the needle with the flat to the back, the needle is properly oriented so that the hook passes behind the cut out. This is crucial for stitch formation, because the cut out increases the size of the thread loop, therefore increases the chances that the hook passes the thread loop successfully, decreasing the likelihood of skipped stitches.
If we accidentally insert the needle the wrong way, where the flat faces the front or the sides instead of the back, the likely result is skipped stitches. Why? Because without the thread loop forming against the circular cut-out, the loop instead will form against the vertical shaft, distorting the shape of the loop. It is much more difficult for the hook to pass through a distorted loop than a proper oval loop.
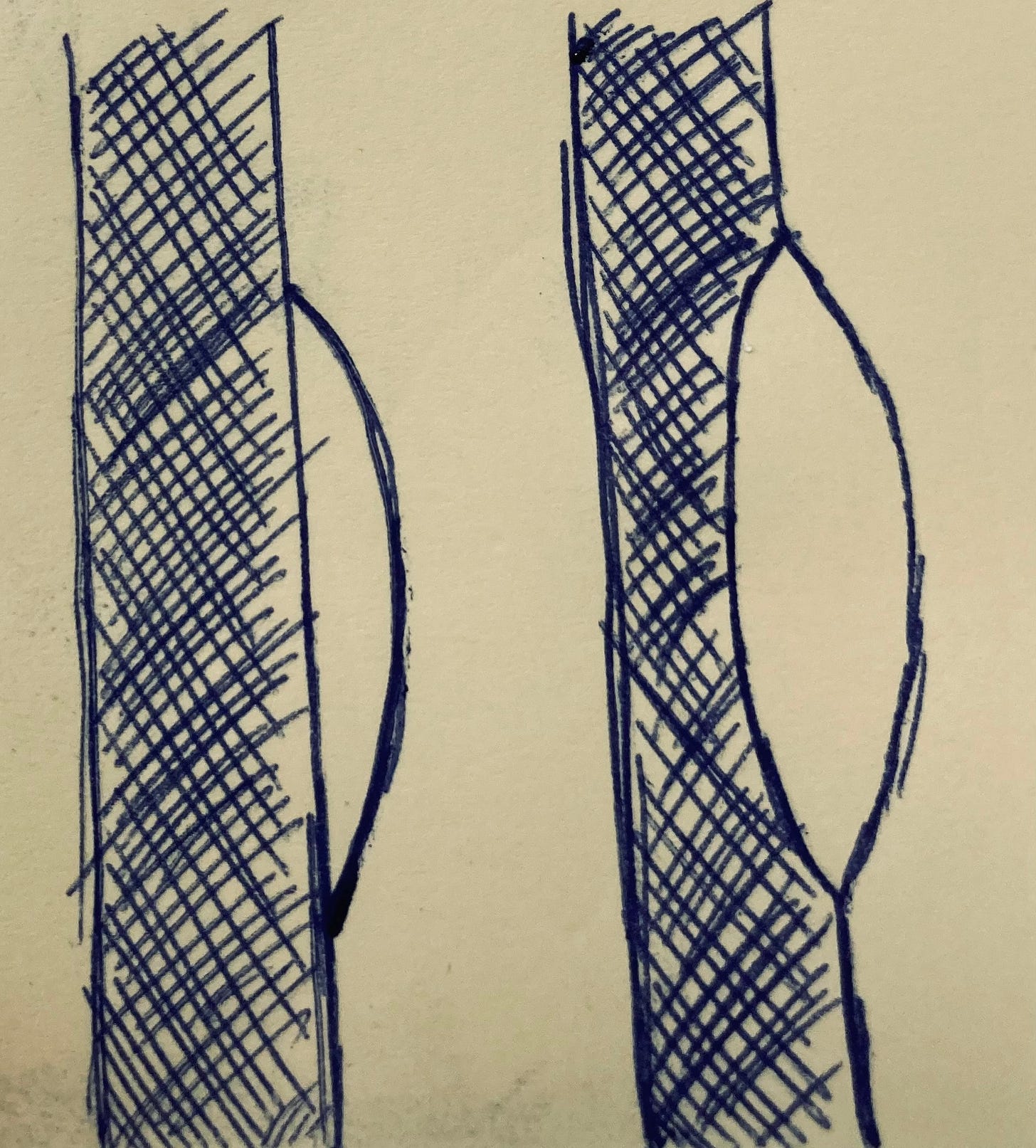
(2) Slide the Needle up all the way
When you insert the needle into the needle clamp, it is crucial that you slide the needle all the way up before tightening the set screw.
As seen in the photo below, there is a pin within the needle bar. When you insert the needle, it must slide all the way up until it hits the pin.
It is a relatively common mistake to accidentally not slide the needle all the way up to the pin. Failure to do so will result in skipped stitches, for a needle not inserted all the way up to the pin will simulate faulty needle-hook timing. It can also result in needle strikes on the hook mechanism, which, if bad enough, will require replacement parts.
(3) Don’t Over-Tighten the Needle Screw
After you insert the needle into the needle clamp, with the flat facing the back and the butt end of the needle slid up all the way to the pin, you will tighten the needle screw so that the needle is secured in place.
The needle screw can be tightened with your fingers; however, because there is not a ton of room in the needle insertion area, the needle screw is often designed so that it can be cinched with a screwdriver.
It is absolutely critical that we do not overtighten the needle clamp screw. It is a set screw, meaning that the screw, when tightened, gets pushed up against the surface of the needle. The force of the screw butted up against the needle shaft is what keeps the needle in place; therefore, the screw only needs to be tight enough to pin the needle. Excessive tightening of this screw is unnecessary and can potentially harm the machine.
The photograph above shows a needle clamp and set screw. The screw was overtightened, causing the tip of the screw to break off inside the needle clamp. The screw tip got stuck inside the clamp, which required a technician to saw off the needle clamp in order to remove the screw tip. Of course, after sawing off the clamp, both clamp and screw had to be replaced. The owner of this particular machine is actually lucky that the screw broke. There have been similar cases of needle screw over-tightening where the screw doesn’t break and goes on to distort the shape of the needle bar, which then must be replaced. Replacing the needle bar is a massive, labor intensive job for a trained sewing machine technician, and a costly mistake for the owner of the machine (I’m talking about hundreds of dollars).
I share this with you to better communicate my earlier point: do not over-tighten the needle screw. Tighten the needle screw as best as you can with your fingers; if you feel like the screw needs to be tightened more, use the screwdriver and give it an eighth of a turn, a quarter turn at most. Anything more than that is excessive.
Thank you for reading. I hope you found this article helpful.
-Cale
Again I learn from the newsletter 😊 I installed a new needle last week and wondered about how much force to use with the screwdriver. No skipped stitches, but I will reinstall the needle today.
Thanks, Karen
Now I understand why it’s so important for the flat side of the needle to face the correct direction!
I never realized that the cut-out (scarf) on the back of the needle plays such a crucial role in stitch formation.
It makes sense that if the needle is inserted incorrectly, the thread loop won’t form properly, making it harder for the hook to catch it and increasing the chances of skipped stitches. This explanation really clarified things for me!
Also, thank you for recommending my Substack—I truly appreciate it!