Troubleshooting strange sounds on a sewing machine
Troubleshooting method for locating unusual sounds on a sewing machine.
When my sewing machine begins making an unusual sound, how do I pinpoint where it's coming from?
Identifying the source of a strange machine sound can be challenging—sometimes it's difficult enough that it requires a trained technician. However, there is a straightforward method you can try at home to diagnose some of the more common sewing machine issues. This approach involves trial and error.
Simply put, you'll systematically remove potential sources of noise, one at a time. If you remove a part and the noise persists, then that particular component is not the issue. If the noise stops after removing a certain part, then you've identified a likely culprit.
So, which parts should you begin checking to isolate the noise? I always recommend starting with the needle.
Needle
Whenever I hear a sewing machine making a strange sound, the first thing I do is remove the needle. Then I run the machine again and listen for whether or not the peculiar sound remains.
A dull needle can cause a “popping” noise when penetrating the fabric. A bent needle may cause a “ticking” noise because it is deflecting off the hook during the stitch-making process. A needle that wasn’t inserted properly may scrape against the floor of the bobbin case basket.
If you remove the needle and the sound goes away, then insert a fresh needle and run the machine again. If you were hearing a “popping” sound caused by a dull needle, then that should go away with a fresh needle.
If you were hearing a “ticking” sound, then that could also go away with a new needle given that the old needle was bent. However, even with a fresh needle there is a chance that the “ticking” sound remains, which indicates that the machine’s needle-hook clearance may be too tight— or that the needle is deflecting off some something other than the hook.
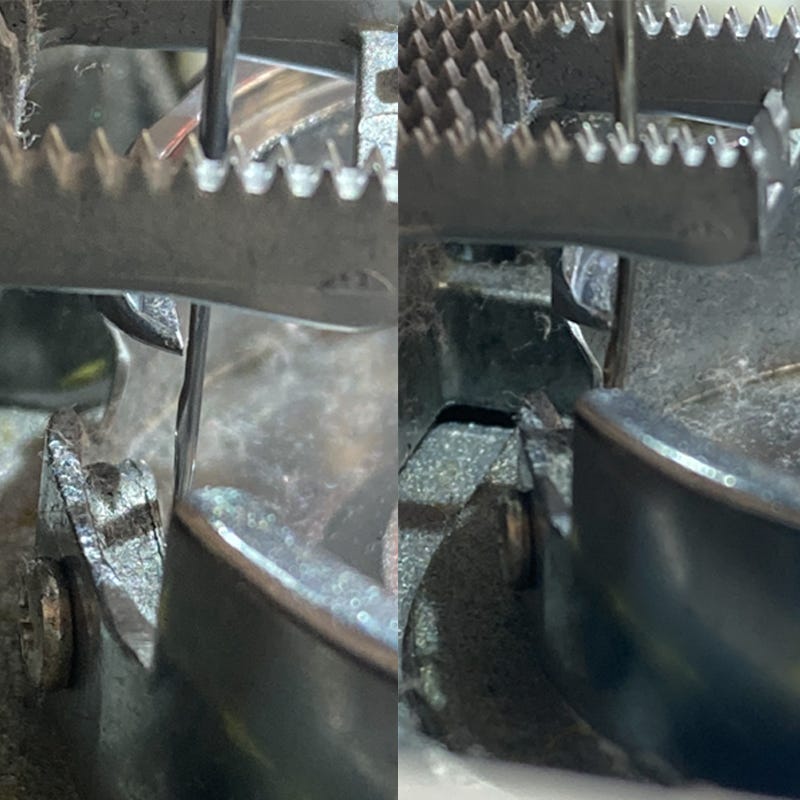
Presser Foot
Though it’s rare, I have seen instances where the needle plate deflects off the presser foot, which would certainly cause a strange sound:
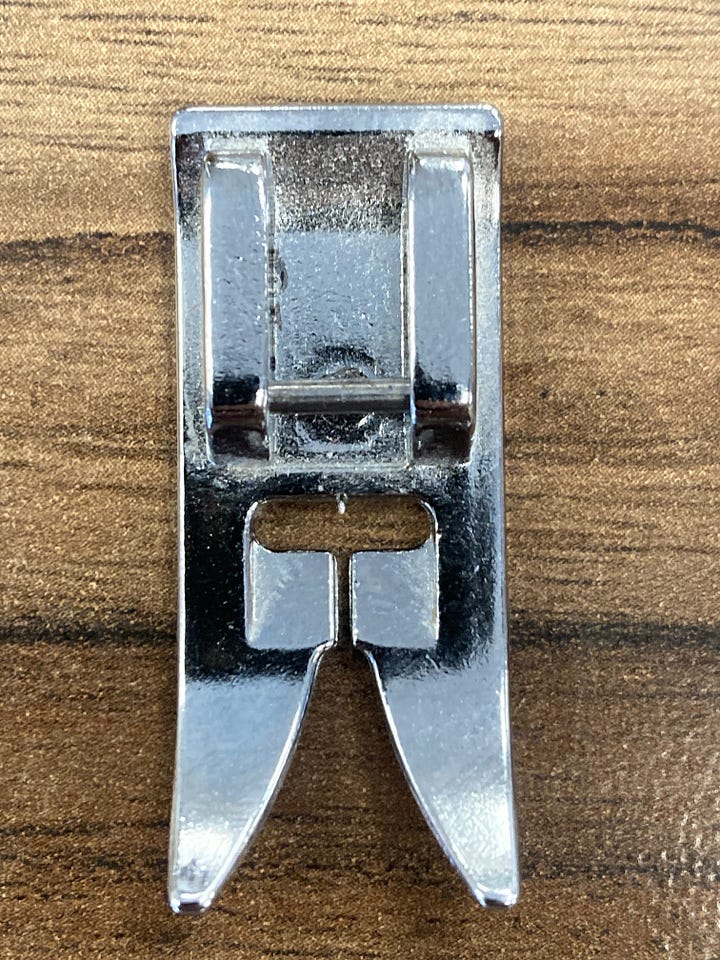
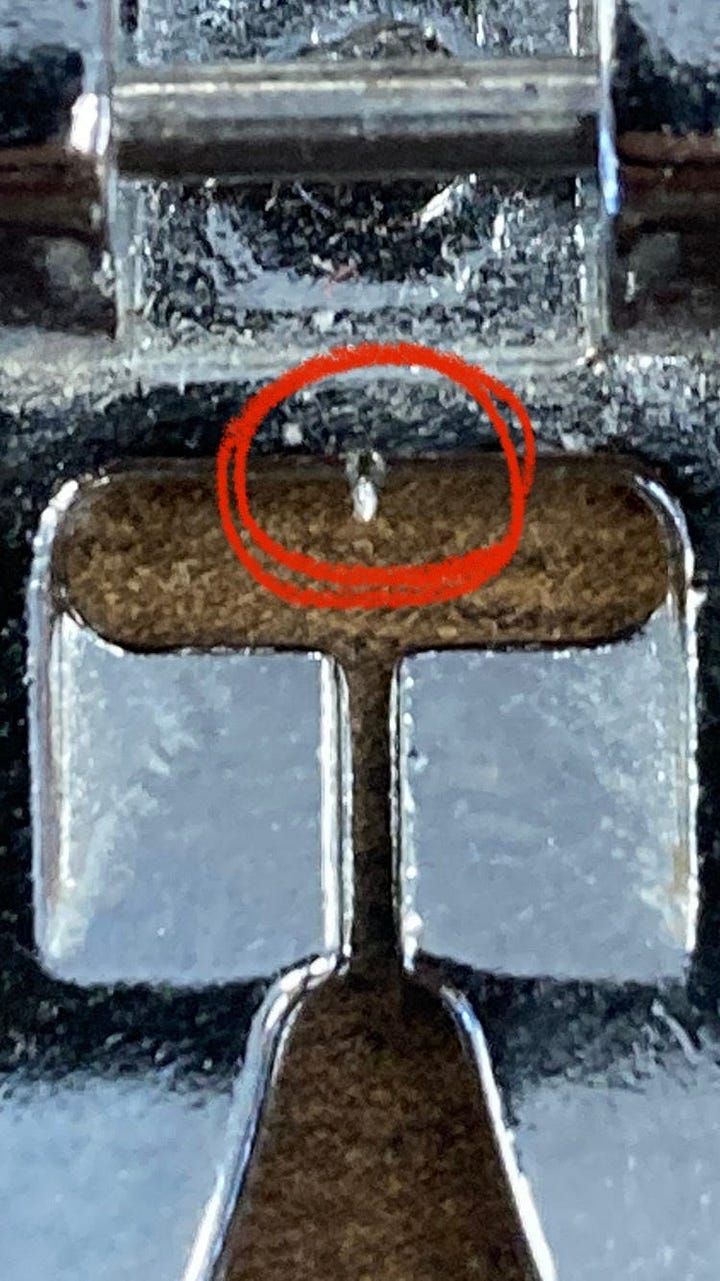
However, the main reason I like to remove the presser foot when troubleshooting is to make sure that the sound I am hearing is not merely the sound of the presser foot making contact with the feed dogs, which is completely normal. An integral part of a sewing machine’s design is that the presser foot holds the fabric down against the feed dogs. If those two parts were not making contact on every stitch, then the machine would not be able to sew.
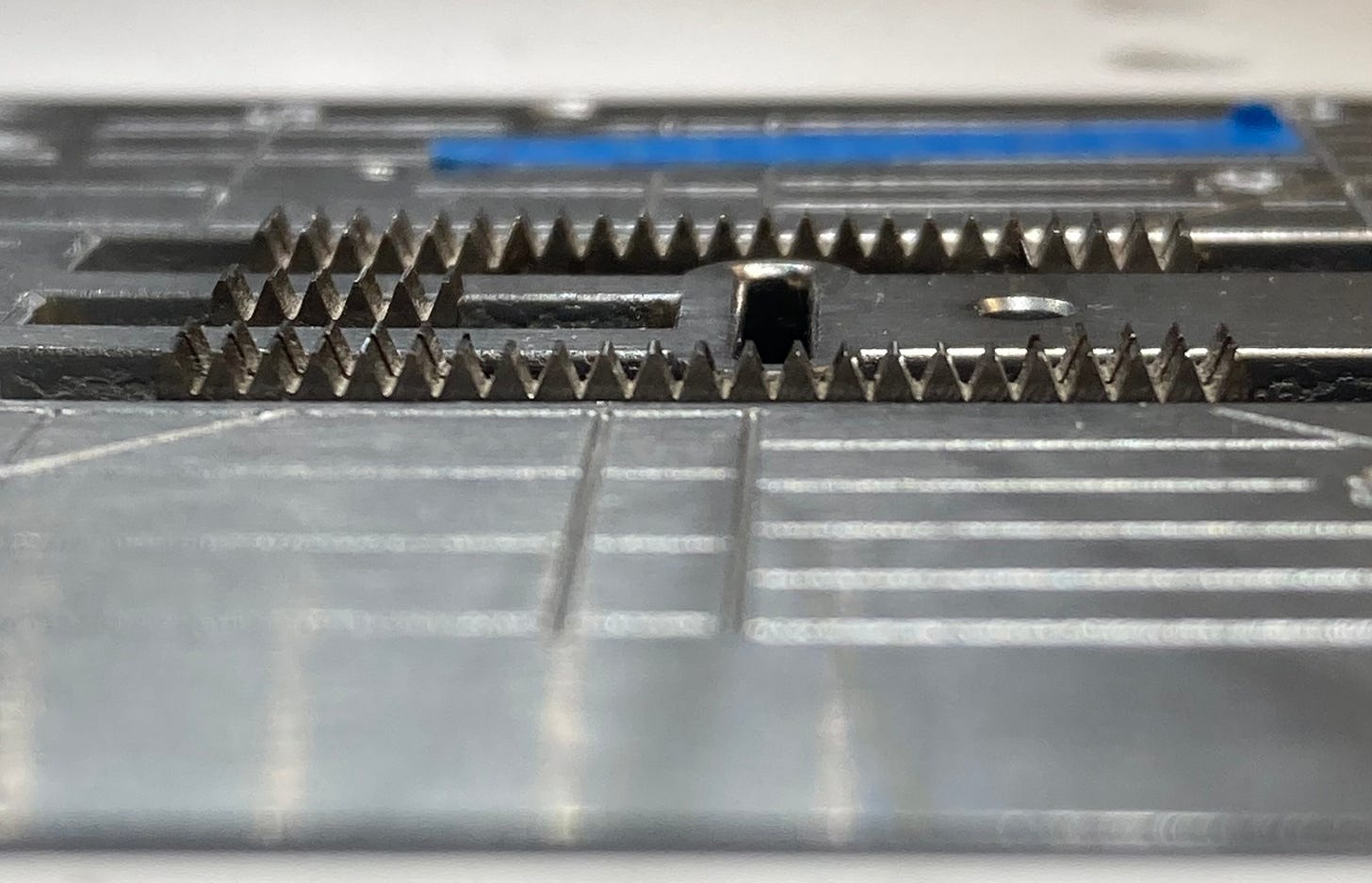
Needle Plate
If the sound isn’t coming from the needle or presser foot, then remove the needle plate and run the machine and see if the sound remains. This is a key part of this troubleshooting process because the needle plate is situated so close to a bunch of different moving parts.
Needle strikes against the needle plate will cause a sound— if you have a fresh needle in the machine and you’re still getting needle strikes on the needle plate, then your needle bar may be misaligned or your needle plate needs to be repositioned.
If the feed dogs are out of alignment, then they may be scraping up against the side of the needle plate.
If needle plate itself is damaged, it could be making contact with the bobbin case. However, even if the needle plate is not damaged, it could still be making contact with the bobbin case, in which case we would need to examine the state of the bobbin case and hook area.
Bobbin Case and/or Hook
Sewing machines designed with a top loading bobbin (horizontal rotary hook machines) are especially susceptible to needle strikes on the bobbin case, which can damage the bobbin case, leading to strange sounds while sewing.
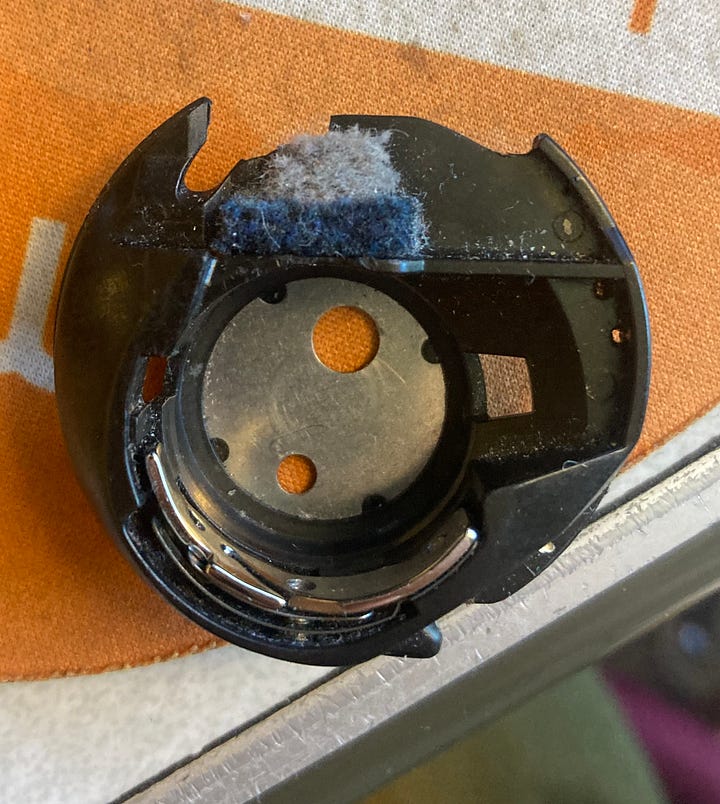
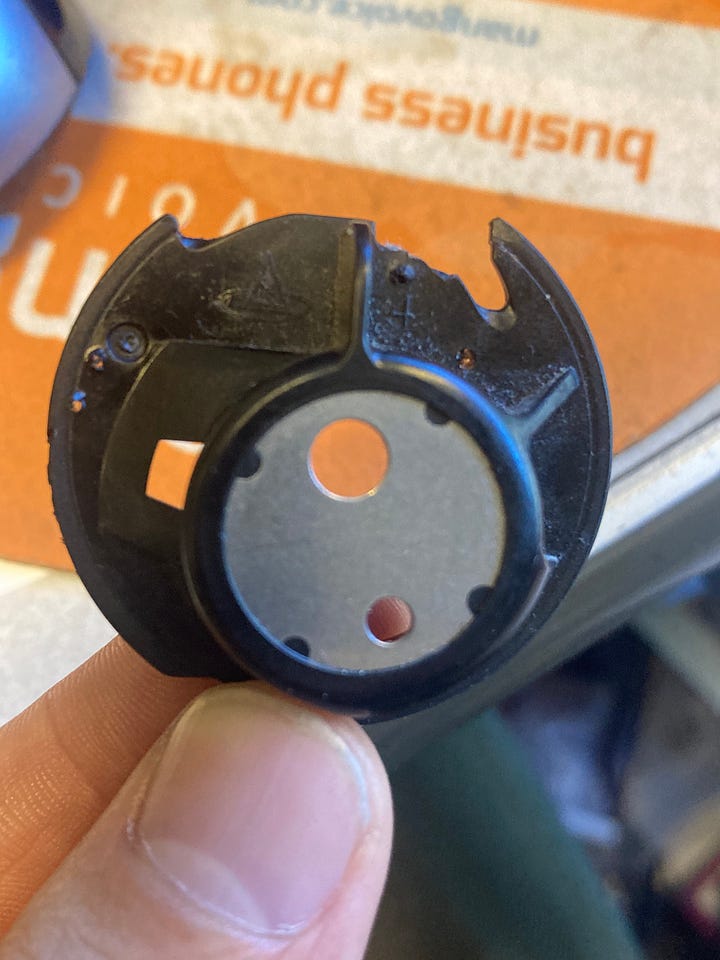
On these horizontal rotary hook machines, the bobbin case sits atop the hook race, which is thin ledge on the inner edge of the hook. The outer rim of the bobbin case makes contact with the hook race.
The outer rim of the bobbin case makes contact with the hook race. Both parts are designed to reduce friction, with the hook made out of a smooth metal and the bobbin case is made out of a smooth plastic. However, a significant needle strike to the bobbin case can damage the shape of the underside of the bobbin case, distorting it in a way so that the hook no longer rotates smoothly underneath. Instead, the increased friction of the hook rotating under the distorted bobbin case will cause a scraping sound that did not exist before.
Depending on the severity of the needle strike(s), the bobbin case may or may not be able to be repaired. If the needle strike is minor, then it is possible to smooth out the burr on the plastic bobbin case with emery tape. If the burr cannot be smoothed out, then the bobbin case will have to be replaced.
Sometimes, removing the bobbin case will get rid of the sound, but not because of a damaged bobbin case. It is possible for the hook race itself to be damaged with a burr in the metal, which scrapes against the bobbin case and generates a scraping sound. If you find a burr on the hook race, it can be really difficult to smooth it out with emery cord. Even for a trained technician, sometimes the burr is bad enough that the entire hook will have to be replaced.
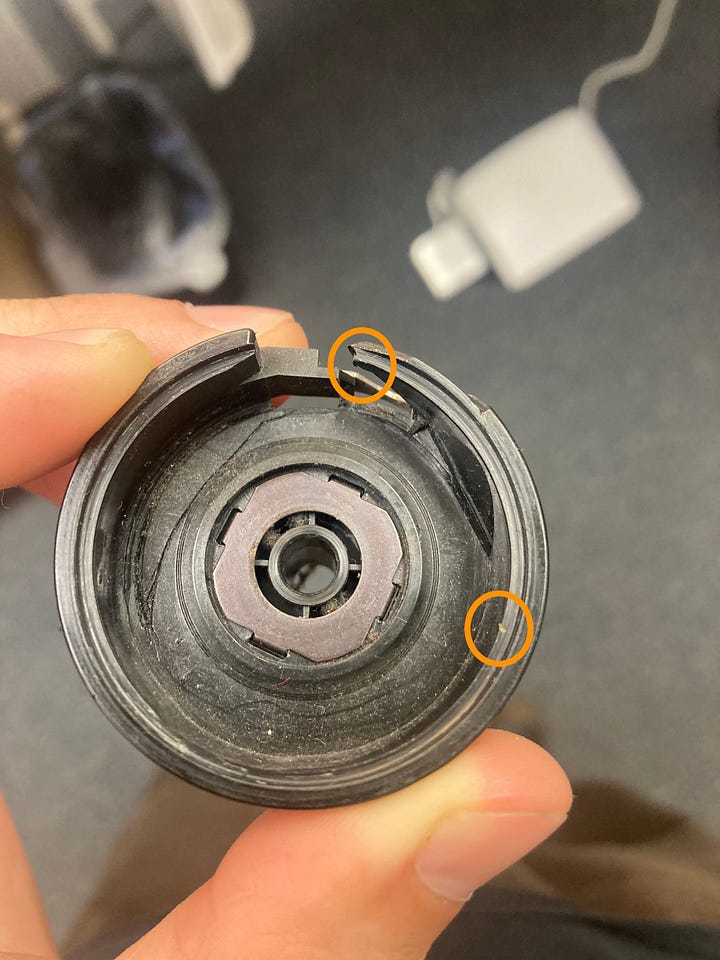
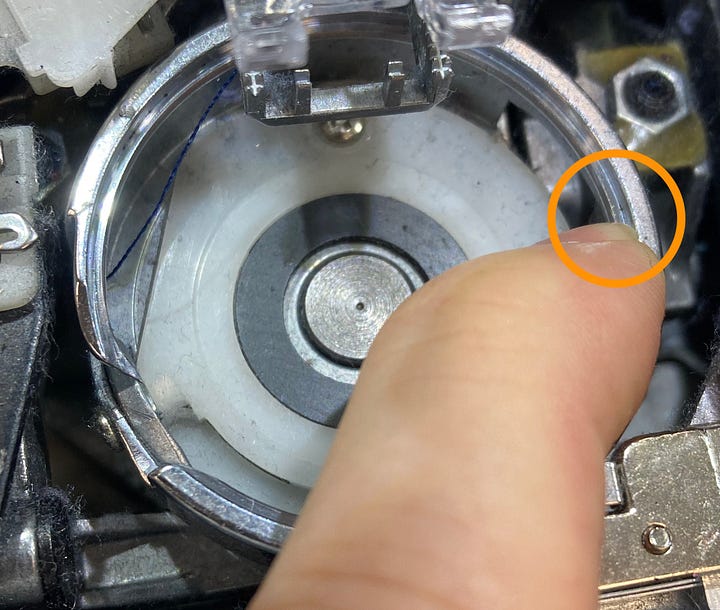
All the same issues with the hook and bobbin case are also possible or sewing machines where the bobbin loads from the front— vintage Pfaff, vintage Bernina, modern Bernina — though it’s much more rare. These machines tend to be loud, but the most common reason for the noise is that the hook race is dry and in need of lubrication.
If you have one of these machines and it seems to be sewing loud, try lubricating the hook race with a drop of oil, then run the machine again and see if the sound goes away.
Thank you for reading!
I hope you found this article helpful. If so, please feel free to share with your fellow sewists! Also, don’t forget to like, comment, subscribe, and explore the archive of more than 100 other sewing machine educational articles.
Thank you.
—Cale
these are great tips with clear explanations. Since I work alot with older, vintage machines (1910-1970 era machines), I often find the noises that are hardest to diagnose aren't in and around the needle and bobbin area - they are often in the drive areas (belts, motor, etc) or metal-on-metal lubrication issues. It's often hard to discern exactly where the sound is coming from. I wonder if you have any tips, aside from the process of elimination you've described, to track down that irritating squeak or squawk or clicking sound coming from somewhere in the machine. I had an experienced tech tell me he will put the end of his screwdriver against different areas of the machine, run the machine and listen to the top of the handle of the screwdriver (apparently it transmits vibrations up the shaft of the screwdriver) and that this sometimes helps him microlocate the source of the sound. Curious if you or anyone in your shop has a similar method...
This is fantastic! Thank you so much for outlining these steps. I do some of the steps but in a haphazard order, so this is a much better way!